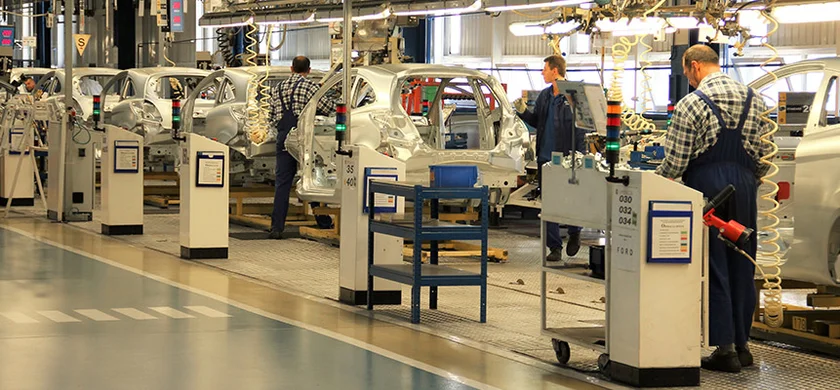
Why Factories and Warehouses Should Be Maintained Clean and How?
A clean environment can decrease employees' risk for sickness. The bacteria thrives at work because the employees spend countless hours there. Keeping your workplace clean may also decrease sickness.
Maintaining a tidy warehouse may require more effort than anticipated, but the benefits are worth it. For one, it can significantly improve performance. A well-organized workspace allows workers to easily locate supplies and equipment, leading to increased productivity and efficiency.
Additionally, it can enhance staffing efficiency as workers become accustomed to working in a familiar environment. It's essential to prioritize safety by following established rules and guidelines.
Impact of Cleanliness: Case Studies
Several case studies have shown the positive impact of maintaining cleanliness in manufacturing facilities. For instance, an automotive manufacturing company saw a 15% increase in productivity and reduced machinery breakdowns by implementing strict cleaning protocols. In a food processing plant, rigorous hygiene practices led to a 30% decrease in product contamination incidents and improved customer satisfaction. A pharmaceutical manufacturing facility achieved a 50% reduction in microbial contamination and fewer product recalls through a comprehensive cleaning plan and proper training.
These examples highlight the tangible benefits of prioritizing cleanliness in the workplace.
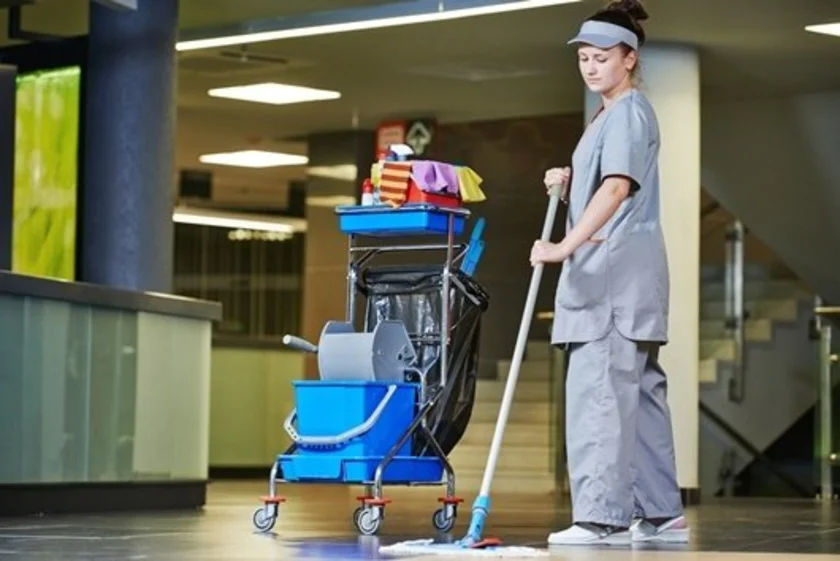
Why a Clean Workplace is Good for Business
The first impression is crucial, and a tidy work environment is not only visually pleasing, but it also creates a welcoming atmosphere. This helps to establish trust and confidence right from the start, showing that attention to detail and efficiency are important. Conversely, a dirty floor or shabby conference chairs can make clients question the professionalism of those who manage the space. Similarly, a cluttered reception area can create a chaotic feel. It's essential to project a positive company image, and a clean workspace can help consumers associate your brand with high-quality products. Consumers associate your brand with high-quality products.
Factory and warehouse premises are frequently viewed as the 'backend' premises of commercial organizations, rarely accessible to consumers and customers. The idea generally persuades management to disregard adequate maintenance. Below are some of the mishaps that can happen if the cleaning protocols are not followed:
Machine lifecycle
Without proper maintenance, expensive machines, tools, and equipment can gather dust and become prone to improper handling and events such as corrosion. This progressively reduces their efficiency and lifespan, necessitating repeated repairs and replacements.
Facility managers should be in charge of monitoring an organised workplace and ensure that the machinery is cleaned regularly.
Productivity
An disorganized production or warehousing environment can significantly reduce overall business productivity. Workers struggle to identify badly kept machinery or delays in loading cargo for delivery to dockyard are some of the consequences.
Employee satisfaction
Employees working at a disorderly or filthy location may not feel the pride or pleasure they expected when they joined your firm. On the other side, providing clean workwear and a clean workplace will keep them motivated and loyal.
Encourage to clean up a messy work environment will upkeep and maintain the employee morale. Providing cleaning resources will help employees adjust to the new norm without feeling pressured to need to know everything beforehand.
Health and safety
Untidy floors after each shift, as well as waste and liquids left unattended, can pose major safety risks to industrial and warehouse workers. Negligence may lead to workplace injuries, which can cost your company a lot of money as well as employee time.
Contamination may occur at a place that handles food, medicines, dairy, and other products due to dirt, dust, and the presence of molds and pests. Workers handling these materials without gloves and masks may increase the dangers.
How to make maintaining a clean warehouse or factory part of your company culture
Making sure staff members and employees are all on the same page about the cleaning process that has to be taken place in the comoany is the one thing that will prevent a messy workplace.
Routine Inspections of Workspaces & Common Areas
To prevent incidents and illnesses, it's important to schedule regular inspections of work areas. Conducting routine inspections in the office can help identify potential hazards that require immediate attention. Moreover, inspections provide employees with an opportunity to express their concerns and offer suggestions. They also help to better understand how work is performed and can assist in identifying and minimizing potential risks. It's essential to take into account any factors that may lead to unsafe or unhealthy situations due to exposure or misuse.
Prohibit Food in Certain Areas
To ensure a clean work environment, it is crucial to eliminate cross contamination of food in the workplace cleanliness. Designated areas where your employees can take a break and enjoy their meal or snacks is best.
Overall productivity will be increased if your employees have a designated area and time slot where they can eat without being rushed back to work.
Making a factory or warehouse cleaning plan
To ensure a clean and organized workspace, it's important to perform both regular and deep cleaning. The level of cleaning required will vary depending on the type of work conducted. Over time, the floors of a warehouse can accumulate dust, so it's essential to schedule periodic deep cleaning to prevent buildup. The frequency of deep cleaning will depend on the nature of the work and may vary across different locations.
Stock Up on PPE & Cleaning Supplies
To ensure a safe and hygienic workplace, it is important to set up a specific area for personal protective equipment and cleaning supplies. Regularly stocking and checking these supplies is crucial. Employees should have access to a variety of tools, such as cleaning machines, gloves, and sanitary wipes, to minimize the risk of disease transmission and prevent the spread of bacteria and viruses. Additionally, consider exploring the full range of janitorial services for the workplace, including a selection of cleaning products.
- Sanitizing wipes
- Sanitizing spray
Invest into steam cleaners
Steam cleaning has been the favored method for cleaning and disinfecting a wide range of items in recent years, including homes, workplaces, medical facilities, and many various sorts of commercial organizations, as well as all types of automobiles. The cleaning process can be simplified with a steam cleaner since it is able to clean and disinfect high traffic areas at the same time.
Steam cleaning is ecologically beneficial since it requires little or no extra detergents or other chemicals to sterilize and deodorize a wide range of surfaces. The capacity of steaming to destroy and eliminate more than 99% of bacteria, viruses, germs, and other pathogens is its most significant advantage.
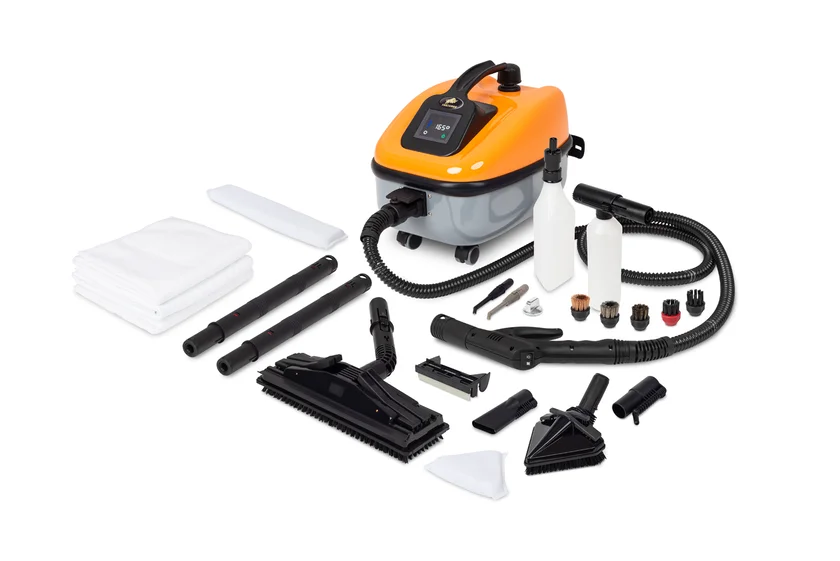
The Fortador Volt Mini is the newest addition to the company's line of steam cleaners. Unlike other compact professional portable steamers for cleaning, the Volt MINI works at high pressure and temperatures, with a maximum temperature of 338 degrees Fahrenheit and a pressure of 101.5 psi. The constructor is constructed of high-strength AISI 304 stainless steel, which ensures its longevity.
With the Volt Mini, you receive a 15-foot hose, which is five feet longer than most other commercial-grade steam cleaning equipment' hoses. With its lengthy power chord, you can get this cleaner into hard-to-reach areas that larger steamers cannot.
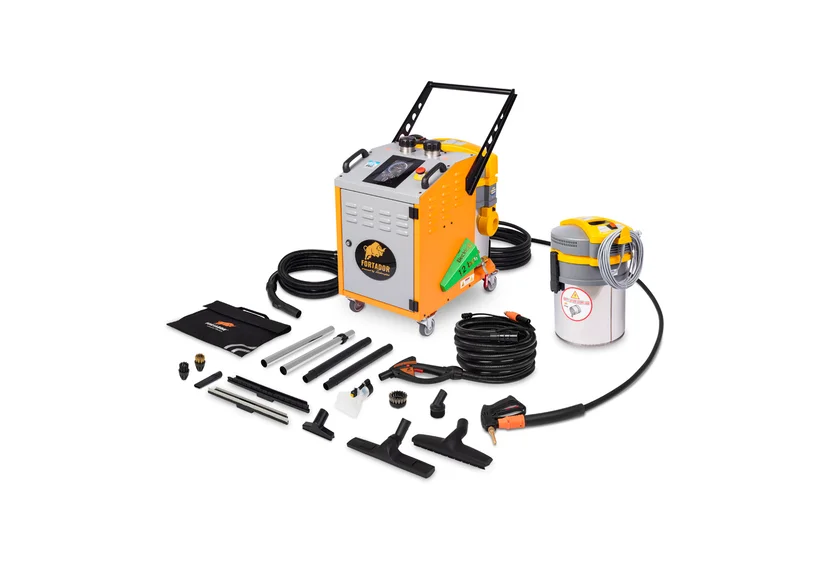
The Fortador Volt Electra is an electric steam cleaner is the world's first totally electric device with a maximum pressure of up to 12 Bar or 175 PSI, which outperforms market-leading diesel combustion engines. Modern design, first-rate craftsmanship while retaining optimum product quality, and corrosion-resistant aluminum wrapped in a single dependable housing.
It is primarily suggested for the provision of private garages, vehicle workshops, and factories due to its relatively tiny cubic capacity. Cleaning firms and hotels like it. Its modest size may be perplexing, yet it is meant to function with two hoses. The Fortador Volt Electra vacuum steamer has two key functions: cleaning and sanitizing with dry steam and extraction using suction and steam plus detergent technology. It includes a quality wet / dry extractor from the respected business Ghibli & Wierbel that can be operated independently.
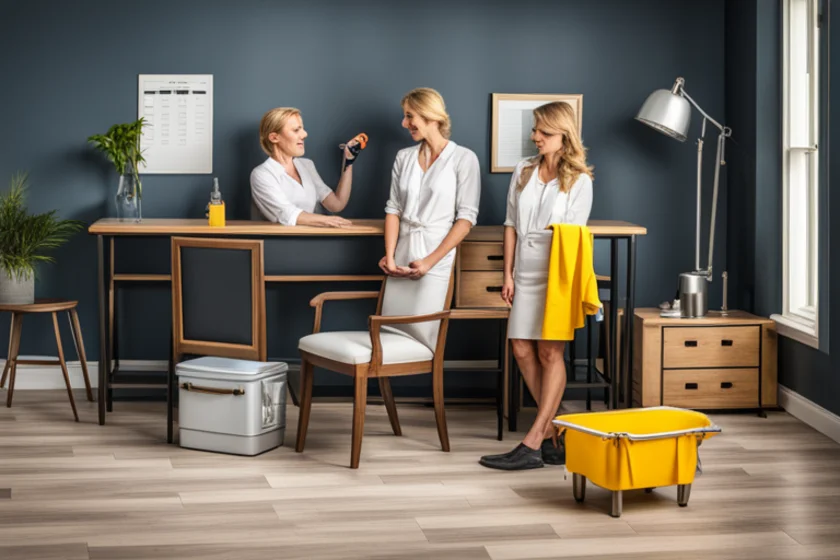
Plan Development
Having a set plan with prevent wasted time looking for the right equipment and cleaning products to upkeep your manufacturing plants, offices and business workplaces.
It may take more effort to build up and keep your warehouse tidy than you think but the result can be worth it. Improved performance First, having the proper workspace will help your workers quickly locate the supplies and equipment they require and directly improve efficiency. It will increase staffing efficiency as they are accustomed to working at the same time. Follow safety rules.
What kind of work you're doing will determine what time of cleaning you will need but you must do two kinds of routine cleaning: regular cleaning and deep cleaning. Cleaning deep In the long run, the floor of your warehouse will become dusty. Your storage room must have an extensive clean before reaching that point. The length of this takes depends upon the type of work you do and could vary for each location.
Implementing Effective Cleaning Protocols
Maintaining cleanliness in manufacturing facilities requires the implementation of effective cleaning protocols. By establishing clear guidelines and procedures, businesses can ensure a consistently clean and healthy workspace for their employees. Here are some key steps to consider when implementing cleaning protocols:
Regular Equipment Maintenance
Regular equipment maintenance is essential for preserving cleanliness and preventing machinery breakdowns. By incorporating routine maintenance tasks into the cleaning protocols, businesses can prolong the lifespan of their equipment while ensuring optimal performance. It is recommended to follow these steps for regular equipment maintenance:
- Create a Maintenance Schedule: Develop a schedule that outlines the frequency and tasks for equipment maintenance. This schedule should be based on manufacturer recommendations and consider the specific needs of each piece of machinery.
- Conduct Routine Inspections: Regularly inspect the equipment for any signs of wear, damage, or potential issues. Look for loose parts, leaks, or unusual noises. Address any identified problems promptly to prevent further damage.
- Clean and Lubricate: Clean the equipment regularly to remove dust, debris, and any contaminants. Use appropriate cleaning solutions and techniques recommended by the manufacturer. Lubricate moving parts as necessary to ensure smooth operation.
- Train Employees: Provide training to employees on the importance of equipment maintenance and proper cleaning techniques. Encourage them to report any issues or abnormalities they notice during their work shifts.
- Document Maintenance Activities: Maintain a record of all maintenance activities, including dates, tasks performed, and any repairs or replacements made. This documentation will help track the history of maintenance and identify patterns or recurring issues.
Preventing Contamination in Manufacturing Processes
In industries that handle sensitive products like food, pharmaceuticals, or electronics, preventing contamination is of utmost importance. Implementing strict cleanliness protocols throughout the manufacturing processes can safeguard product quality and consumer safety. Consider the following measures to prevent contamination:
- Establish Cleanroom Environments: Designate specific areas within the facility as cleanrooms, where stringent cleanliness and hygiene standards are maintained. Control access, airflow, and filtration systems to minimize the introduction of contaminants.
- Follow Good Manufacturing Practices (GMP): Adhere to industry-specific GMP guidelines to ensure hygienic practices throughout the manufacturing processes. This includes wearing appropriate protective clothing, using sterile equipment, and following proper sanitization procedures.
- Implement HACCP Plans: Hazard Analysis and Critical Control Points (HACCP) plans help identify and mitigate potential contamination risks. Conduct a thorough analysis of the manufacturing processes, identify critical control points, and establish protocols to monitor and control contamination risks at each stage.
- Train Employees on Hygiene Practices: Provide comprehensive training to employees on proper hygiene practices, such as handwashing, sanitizing work surfaces, and using protective equipment. Emphasize the importance of following these practices diligently to minimize the risk of contamination.
- Regular Audits and Testing: Conduct regular audits and testing to ensure compliance with cleanliness standards and to identify any potential sources of contamination. This may include environmental monitoring, microbiological testing, or swabbing surfaces for analysis.
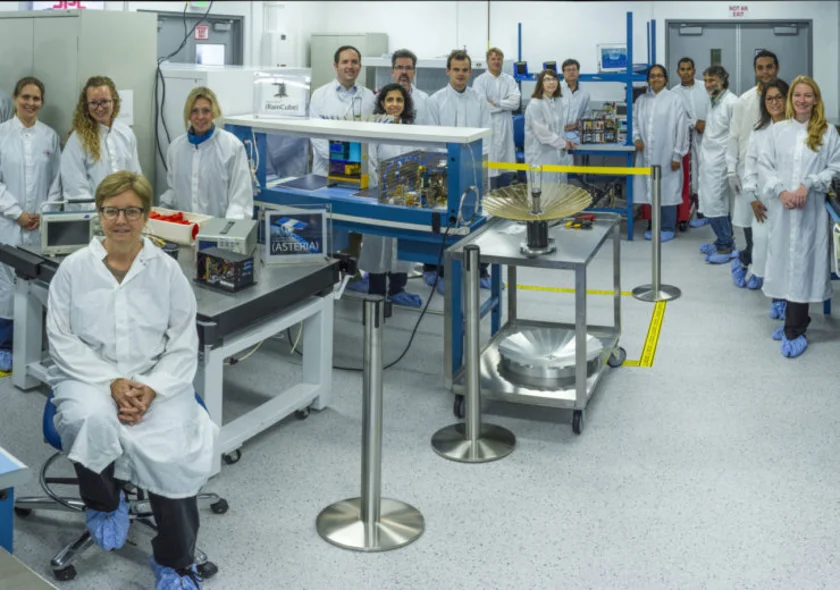
Conclusion
By incorporating these preventive measures into the cleaning protocols, businesses can minimize the risk of contamination, protect product integrity, and ensure the safety of consumers.